Mercedes-Benz is the first
automaker to introduce an electronic brake-assist system which can recognize emergency
braking and automatically apply full-power brake force for shorter stopping distances.
The system, which is activated only in
emergency braking situations and doesnt affect normal brake operation, made its'
debut on many 1998 Mercedes-Benz models.
Why was the BAS Developed?
Many Drivers Dont Apply Full Braking in Emergencies. In tests on their
driving
simulator and on the test track, Mercedes-Benz safety researchers discovered that even
experienced drivers may not apply full braking force in emergency situations.
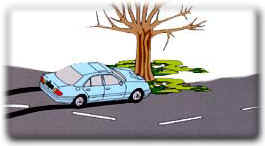
Although the reasons for this are unclear, the solution
is relatively simple: use technology to design a system which can recognize emergency
braking (whenever the pedal is being depressed very quickly), then react with split-second
electronic speed to apply full brake force automatically.
Tests showed that 99 percent of drivers
were slow in applying the brakes or only applied full brake pressure when it was too late.
Mercedes-Benz researchers found that the new brake assist system can provide 45 percent
shorter stopping distances for many drivers, and even skilled drivers find about a 15
percent improvement.
Most drivers took 239 feet to
stop a car from 100 kilometers per hour (or 62 mph), while cars equipped with the new
Mercedes-Benz brake assist system came to a halt in just 131 feet. Even when drivers
applied the brakes very late in an emergency, stopping distance was reduced by nearly 20
feet more than a car length.
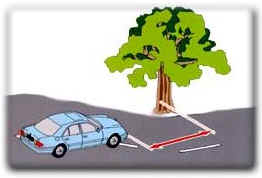
The new Mercedes-Benz brake assist system provide the
critical difference between an accident and a close call because the electronic system can
react far faster than any human.
How It Works
Brake assist is a driver-adaptive system which
learns each drivers braking habits by using electronic sensors to monitor every
movement of the brake pedal and feed information to a mini-computer.
As a result, the system can instantly recognize when
the driver pushes the brake pedal quicker than normal.
If it ever reads pedal speed signals which clearly
mean an emergency, the computer instantly applies an electronic valve on the brake booster
system for full braking. The wheels do not lock because of the presence of the standard
ABS anti-lock brakes, so that the new Mercedes-Benz brake assist system takes advantage of
the safety benefits of ABS.
As soon as the driver eases up on the brake pedal, normal brake control resumes.
To exchange important data at lightening speeds, the
Mercedes-Benz brake assist system networks withother in-car micro-computers for ABS
brakes, ASR traction control or ESP stability control, and the engine/transmission
electronics.
The system even processes information about the
amount of brake wear and vehicle speed. |